Drive Success with Smarter Design
Engineering great products isn’t just about an innovative idea—it’s about ensuring your designs translate seamlessly into efficient, cost-effective manufacturing. This is where Design for Manufacturability (DFM) comes in. By integrating manufacturing considerations early in your design process, you’ll save time, reduce waste, and unlock unparalleled production potential.
Whether you’re creating consumer products, industrial equipment, or high-tech devices, Design for Manufacturability (DFM) ensures that what you envision can be turned into reality—flawlessly and efficiently.
What is Design for Manufacturability (DFM)?
Design for Manufacturability (DFM) refers to the practice of designing products that simplify and optimize the manufacturing process. It involves collaborating closely with engineers, designers, and production teams to ensure that every component is manufacturable, cost-effective, and of high quality right from the start.
By addressing real-world production constraints and challenges during the design phase, Design for Manufacturability (DFM) allows for smoother workflows and overall better outcomes in mass production.
Core Elements of DFM:
- Evaluating the production capability of materials and processes
- Simplifying complex designs to reduce time and effort
- Tailoring designs to fit machinery and manufacturing technology
- Identifying potential production bottlenecks upfront
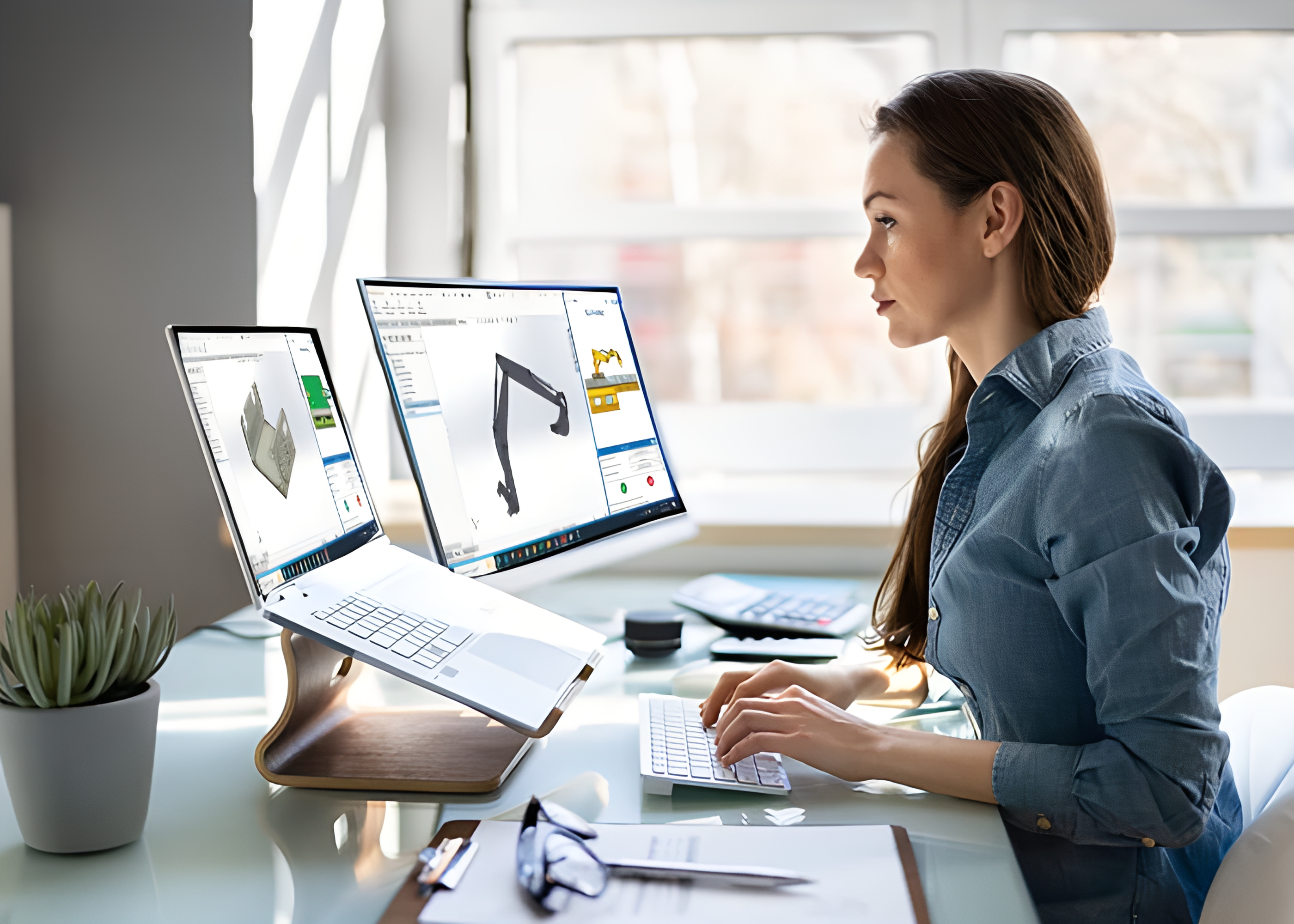
Every strong product starts with a design that doesn’t just look good—but works better where it matters most.
Why is Design for Manufacturability (DFM) Important?
Design for Manufacturability (DFM) plays a critical role in bridging the gap between innovation and production. But why does it matter so much? Here’s why:
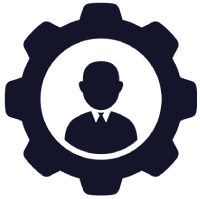
Cost Efficiency
By streamlining designs, unnecessary complexities, and redundancies are eliminated, saving on material and labor costs
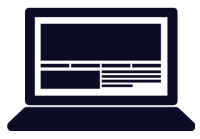
Faster Time-to-Market
Factoring in manufacturability reduces delays in product launches caused by reworks or production inefficiencies.
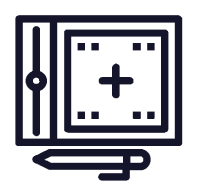
Reduced Waste
With optimized designs, material waste and defective parts are minimized.
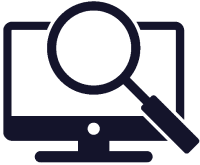
Risk Mitigation
Addressing manufacturing challenges early helps avoid costly issues later in the production phase.
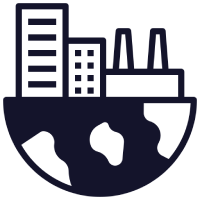
Enhancement of Product Quality
DFM ensures consistency and reliability during mass production, paving the way for better customer satisfaction.
Design for Manufacturability (DFM) is your blueprint for building smarter, scalable, and successful product strategies that deliver on all fronts—be it innovation, quality, or profitability.
Importance of Design for Manufacturability (DFM)
Design for Manufacturability (DFM) significantly reduce change orders manufacturing defects, costs and delays
At its core, Design for Manufacturability (DFM) is guided by a set of practical principles designed to streamline manufacturing and add value to the product lifecycle. Here are some foundational guidelines:
- Material Selection
- Choose cost-effective, easily accessible materials.
- Prioritize materials compatible with existing manufacturing techniques to avoid unnecessary adjustments.
- Simplify Design Complexity
- Minimize the number of parts to avoid assembly errors and costs.
- Aim for symmetry and standardization wherever possible.
- Optimize for Manufacturing Processes
- Design with existing production tools, technologies, and workflows in mind.
- Avoid features that require specialized or non-standard operations.
- Tolerances and Margins
- Set realistic and achievable tolerances to ensure manufacturability without compromising product functionality.
- Modular Design
- Break the product into easily manufactured and assembled modules.
- Ensure modular elements can integrate effortlessly into the final structure.
These principles act as a framework for creating designs that achieve both functional and production goals in harmony.
If integrated correctly, DFM becomes a competitive advantage that differentiates your products and processes from the rest.
Here’s a snapshot of what you stand to gain:
- Long-Term Cost Savings : Solving manufacturability challenges at the design stage reduces production iterations, overhauls, and material wastage.
- Speeds up market entry: Early recognition of an (manufacturability) issue reduces product development time and hence the time taken to market
- Improved Product Lifecycle :DFM ensures your design evolves into a reliable, scalable product fit for sustained production and market expansion.
- Operational Efficiency: Optimized designs improve resource utilization, ensuring you extract maximum value from your existing systems and machinery
- Boost to Innovation: With manufacturing obstacles minimized, your team can focus on creative solutions and breakthrough designs.
- Customer Satisfaction: Smoother production cycles, reliable products, and reduced defects mean better experiences for your customers.
Good design doesn’t just solve a problem; it sets the foundation for seamless execution, ensuring your visions come to life without compromises.
Case Study 1: Consumer Electronics
Problem: A startup struggled with high unit costs during the mass production of a new smart device.
Solution: Implementing DFM principles reduced unnecessary assembly steps, cutting material usage by 12% and saving $80,000 annually.
Case Study 2: Automotive Sector
Problem: Production bottlenecks caused shipment delays in a tier-1 supplier’s manufacturing plant.
Solution: DFM-led redesign streamlined part compatibility and reduced assembly time by 25%, allowing the plant to meet its deadlines consistently.
Case Study 3: Medical Equipment Manufacturers
Problem: A precision medical component had a high rejection rate during manufacturing.
Solution: By revisiting the tolerances and simplifying design features, the rejection rate decreased by 40%, significantly improving operational output.
These stories testify to the tangible value DFM brings across industries, solving both small-scale and complex production challenges.
Turn Your Ideas into Production-Ready Designs
Every product starts with an idea. But transforming that idea into a successful outcome? That’s where DFM shines.
Whether you’re redesigning existing products or starting fresh, integrating DFM ensures you reduce costs, avoid manufacturing headaches, and deliver quality that stands out in the market.
Want to see how DFM can elevate your projects? Contact us today to explore custom solutions tailored to your needs.
-
Standardization of Components
-
Simplifies manufacturing processes
-
Design for Testing and Quality Control
-
Design for Automation
-
Design for Digital Manufacturing
Resources
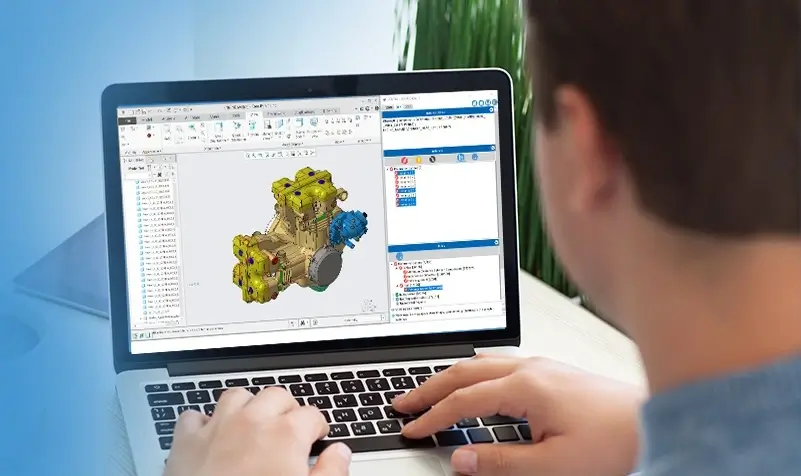
Designing for Manufacturability: How Alcon saves time and reduces cost with Creo and DFMPro
Learn from Alcon a pioneering medical manufacturer of eye care components on how they have achieved early visibility into the manufacturability and could save time to market and reduce the product cost with DFMPro and Creo.
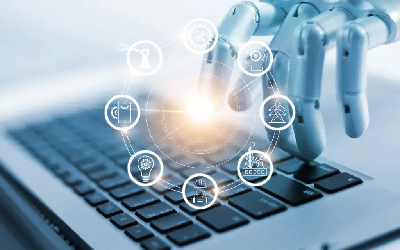
Watch On Demand Webinar – Design for Manufacturing: A Critical Digital Transformation Element
Digital transformation is a significant trend in manufacturing companies and requires new automated ways to leverage digitalized information.
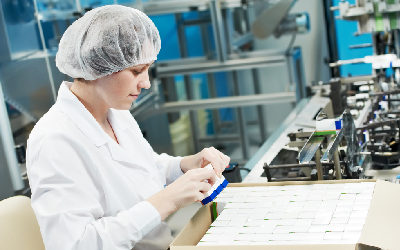
Special Considerations in Designing Medical Products
This whitepaper looks at the key considerations when designing injection-molded medical devices.