Designers are tasked not only with satisfying functional requirements, but also manufacturability requirements. Requirements might include keeping product costs within the budgetary constraints and delivering innovative solutions to customers. But new or inexperienced designers, especially those unfamiliar with manufacturing process requirements and downstream related parameters and constraints, may unwittingly cause costly rework. Almost 30–35% of engineering rework on a global average occurs because of downstream manufacturability issues occurring late in the cycle.
Some of the typical issues observed are plastic parts missing drafts, non-uniform wall thickness, sudden variation in wall thickness, inappropriate bosses and rib designs, no consideration for thin steel condition, etc. These issues lead to issues like defective parts, warpage, and frequent field failures. Ultimately, these issues lead to part rejection, rework, delay in delivery, and increase in overall product cost. Some of the design conditions also lead to increased tooling cost.
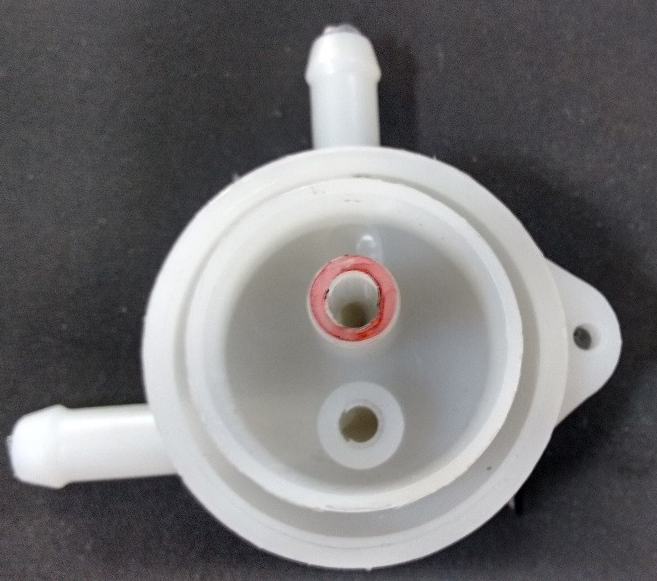
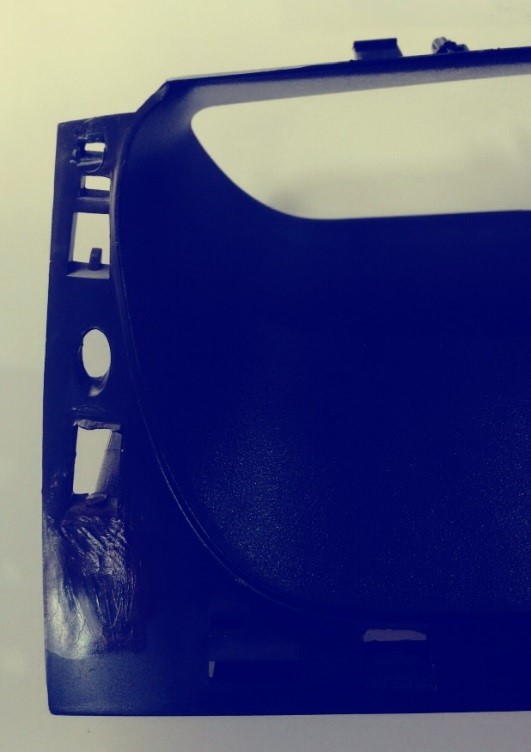
Various studies have shown that errors rectified during the design stage can cost a hundred times less than errors detected during the manufacturing stage. But if designers are inexperienced or unfamiliar, how can they rectify errors they don’t know they’re making? There are three significant ways to manage that question:
1- Implement DFM
Manufacturers avoid considerable costs with engineering rework when Design for Manufacturing (DFM) methodology is incorporated as part of the product development process. Design for Manufacturing knowledge plays a vital role in controlling product costs and maximizing engineering productivity by addressing potential problems in design phase itself.
Some of the typical methods of DFM implementation are:
- DFM checklists and handbooks
- Classroom training on DFM best practices
- Expert discussions and reviews
- Dedicated validation teams
- Hiring consultants for design review
To reduce defects, cut down rework, eliminate waste, shorten time to market, and save costs, DFM guidelines must be implemented early in the product development phase. That said, best practices like the above list can be time-consuming to incorporate. Luckily, there’s an easy answer to that.
2 – Automate DFM
An automated solution that can take the place of manually reviewing designs for hundreds of design guidelines will cut human-made errors and free up limited time and resources. Some of the benefits that can be achieved through an automated DFM solution are:
- Improved time-to-market
- Faster decision on manufacturability issues
- Direct and indirect cost savings associated with design iteration
- Cost savings associated with rework and scrap
- Capturing and re-use of best practices and tribal knowledge for continuous improvement
- Improved collaboration between designer and suppliers
3- Choose the Right Automated DFM
To truly reduce engineering rework, a smart automated DFM tool should be implemented. Tools like DFMPro can easily automate the design for manufacturing guidelines within your CAD software and automatically review designs for downstream manufacturability, supplier capability, assembly, cost, quality etc. Designers can quickly ensure whether their designs can be easily manufactured, who is the best supplier to manufacture it, and whether if any design feature will increase the cost significantly.
DFMPro can help in better understanding of downstream requirements at the right time – that is, when the design is being created. It further promotes collaboration of design with manufacturing, and captures the right understanding of supplier capability to design parts the very first time. This drastically reduces the review time and avoids rework in design. Using DFMPro, you can improve engineering productivity by over 15%.
To reduce engineering rework and prevent costly design fixes, consider automating with a powerful tool like DFMPro, which reduced product costs and improves time to market. Contact us now to begin your journey.