Design Guidelines for Bosses
Minimum Radius at Base of Boss
Boss, a basic design element in plastics, is typically cylindrical and used as a mounting fixture, location point, reinforcement feature or spacer. Under service conditions, bosses are often subjected to loadings not encountered in other sections of a component. Provide a generous radius at the base of the boss for strength and ample draft for easy part removal from the mold. A fillet of a certain minimum radius value should be provided at the base of boss to reduce stress. The intersection of the base of the boss with the nominal wall is typically stressed and stress concentration increases if no radii are provided. Also, the radius at the base of the boss should not exceed a maximum value to avoid thick sections. The radius at base of boss provides strength and ample draft for easy removal from the mold. It is recommended that the radius at the base of boss should be 0.25 to 0.5 times the nominal wall thickness.
Boss Height to Outer Diameter Ratio
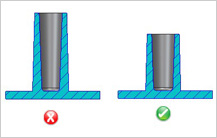
A tall boss with the included draft will generate a material mass and thick section at the base. In addition, the core pin will be difficult to cool, can extend the cycle time and affect the cored hole dimensionally.
It is recommended that height of boss should be less than 3 times of outer diameter.
Minimum Radius at Tip of Boss
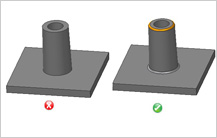
Bosses are features added to the nominal wall thickness of the component and are usually used to facilitate mechanical assembly. Under service conditions, bosses are often subjected to loadings not encountered in other sections of a component.
A fillet of certain a minimum radius value should be provided at the tip of boss to reduce stress.
Wall Thickness of Boss
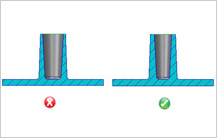
Wall thicknesses for bosses should be less than 60 percent of the nominal wall to minimize sinking. However, if the boss is not in a visible area, then the wall thickness can be increased to allow for increased stresses imposed by self-tapping screws. It is recommended that wall thickness of boss should be around 0.6 times of nominal wall thickness depending on the material.
Radius at Base of Hole in Boss
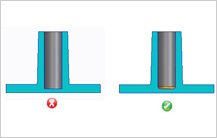
Bosses find use in many part designs as points for attachment and assembly. The most common variety consists of cylindrical projections with holes designed to receive screws, threaded inserts, or other types of fastening hardware. Providing a radius on the core pin helps in avoiding a sharp corner. This not only helps molding but also reduces stress concentration. It is recommended that the radius at base of hole in boss should be 0.25 to 0.5 times the nominal wall thickness.
Minimum Draft for Boss Outer Diameter and Inner Diameter
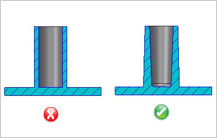
An appropriate draft on the outer diameter of a boss helps easy ejection from the mold. Draft is required on the walls of boss to permit easy withdrawal from the mold. Similarly, designs may require a minimum taper on the ID of a boss for proper engagement with a fastener. Draft is required on the walls of boss to permit easy withdrawal from the mold. It is recommended that minimum draft on outer surface of the boss should be greater than or equal to 0.5 degree and on inner surface it should be greater than 0.25 degrees.
Spacing between Bosses
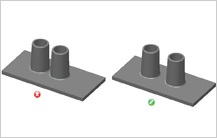
When bosses are placed very close to each other, it results in creating thin areas which are hard to cool and can affect the quality and productivity. Also, if the mold wall is too thin, it is very difficult to manufacture and often results in a lower life for the mold, due to problems like hot blade creation and differential cooling. It is recommended that spacing between bosses should be at least 2 times the nominal wall thickness.
Bosses and other thick sections should be cored. It is good practice to attach the boss to the sidewall. In this case the material flow is uniform and provides additional load distribution for the part. For better rigidity and material flow, the general guideline suggests that boss should be connected to nearest side wall.