How can DFMPro Help Business Continuity in Today’s Changing Industry Landscape?
COVID-19 has brought upon unprecedented challenges for global industries that are looking at redefining their business models for business continuity. Leaders are faced with uncertainties on executing their programs with the desired Quality on time and within budgets in the new normal, due to dispersed functional teams. The risk of quality escapes and engineering changes are a force multiplier in terms of its negative impact .
A software driven digital manufacturing assistant , that helps in first pass yield , meeting the quality and cost standard is a game changer.
DFMPro provides distinct benefits for companies trying to realign their design and production to meet the changing economic and political landscapes. If you are looking for solutions that can bring in design efficiency, increase in productivity and better management of in house-manufacturing or supplier base, without affecting time to market and cost targets, DFMPro has you covered.
DFMPro is about streamlining processes with knowledge capture, reuse, and deployment in a non-intrusive manner, something particularly critical when you consider remote manufacturing.
Virtual Collaboration With Manufacturing And Suppliers
DFMPro enables seamless virtual collaboration between design groups and manufacturing (in-house or global suppliers) for uninterrupted product development even during major shutdowns.
Maintain social distancing norms for safety of the workforce
“Through Digital Manufacturing Assistant” that bring design, review (validation) and manufacturing teams closer via the virtual space, and the Manufacturability issues are software enabled right at designer desktop.
Eliminate delays in getting right feedback
Designers need quick validation to release parts for production. DFMPro assists with an effective review mechanism enabling clear and concise messaging that aids corrective decisions for faster product release.
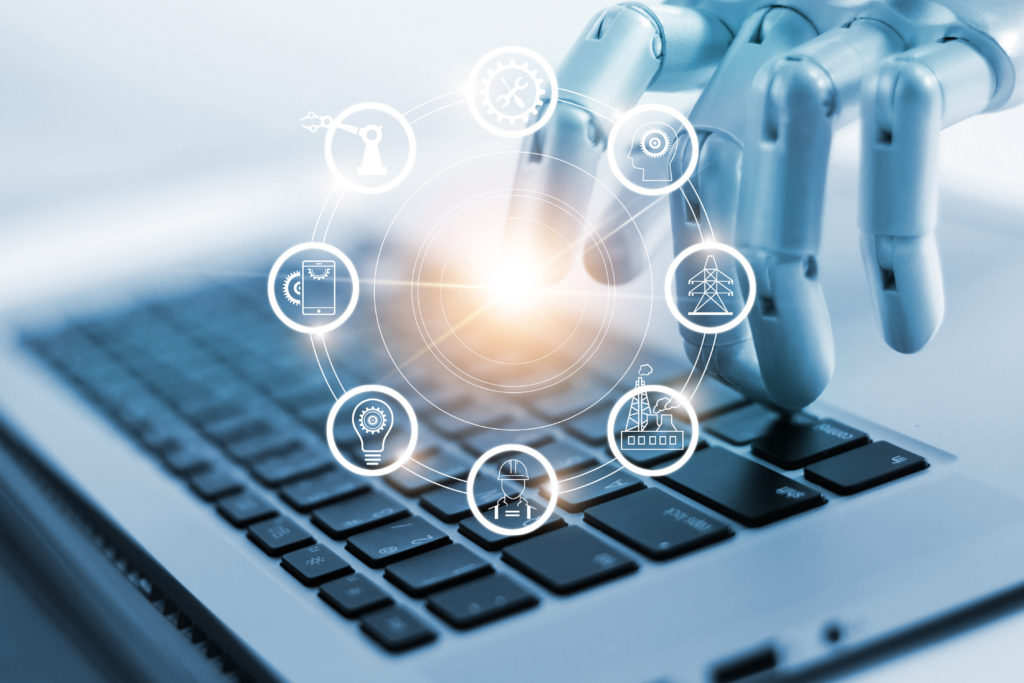
Design for Excellence (DFX) Survey
See how organizations are moving towards DFX practices and current state of DFX process maturity in organizations.
Re-Alignment Of Supply Chain In Covid World
COVID-19 crisis has forced many organizations, to rethink and re-align their supply base. It has exposed the vulnerabilities of many organizations, especially who depend on suppliers globally distributed. This also means switching supplier base, capacity and being flexible in terms of capacity in such trying times. This process of re-aligning with suppliers to make sure these components are easy, quick, and economical to manufacture is key to the success.
One of the biggest impediments, in re-alignment is manufacturability. Due to shear nature of product design, the components are sent to a supplier and manufacturability feedback is given by the supplier to design team. This process is iterative in nature as reviews are done over several meetings or even in person at suppliers manufacturing location.
The COVID situation is causing significant disruption in this manual review process. Collaboration is challenging as communicating with new supplier and understanding the capability to get design out that is compatible for manufacturing will take more months.
Adopting DFX methodology to quickly re-align supply chain
- Quickly capture organization best practices and evaluate designs that meets supplier capabilities
- Reduce no of design reviews and save the time and effort on design iterations
- Find out most suited parts to manufacture for a given supplier from existing base
Quick on-boarding of new suppliers
- With today’s trend of outsourcing both design and manufacturing of components to suppliers, its important that supplier should follow design best practices recommend by the OEM
- DFMPro helps in capturing OEM organization’s best practices and adherence of the same by suppliers
- This helps in reduces learning time for suppliers and quickly on-boarding them
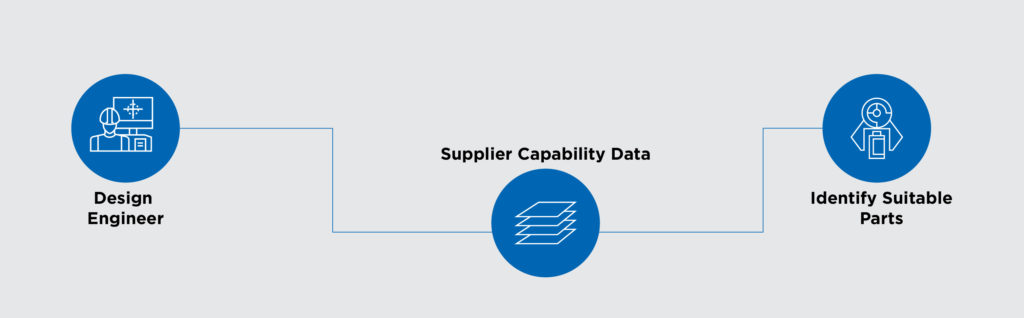
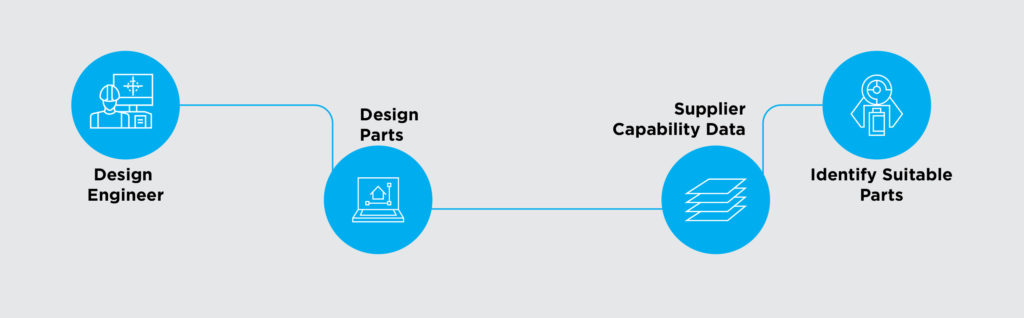
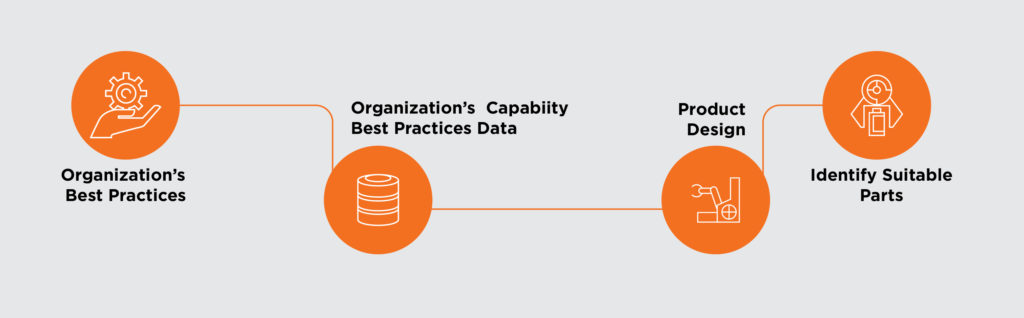
Knowledge Capture And Reuse– Bring In Standardization
The COVID-19 pandemic is already causing a host of challenges to industrial manufacturers. About 80% of manufacturers expect that the pandemic will have a financial impact on their business, according to a recent survey of the National Association of Manufacturers (NAM). Many industries are poised to or have already slashed workforce to face the economic crisis. High paying jobs like those of mechanical designers are at most risk. Availability of experts and their knowledge is the biggest problem for organizations.
Having an automated mechanism to capture organizations’ best practices and tribal knowledge is very critical to maintain business continuity in crisis. Current design approaches to address downstream requirements are a combination of many different ways including reference handbooks, product and industry standards checklist, cross-functional reviews, or design engineers’ tribal knowledge. Yet, rework and engineering changes happen too often late in the cycle, especially when they become expensive and time consuming to correct.
Getting designs right first time for multiple downstream requirements can be complex, and daunting. DFMPro provides an environment to capture and formalize best practice knowledge.
- Capture knowledge of experts and make sure it’s available to everyone all the time!
- Out-of-Box industry best practices available in form of DFM rules for core manufacturing processes like Machining, Injection Molding, Sheet Metal Fabrication, Casting and Assembly
- Highly customizable DFM frameworkto capture and integrate in-house knowledge and best practices in form of structured rules into the overall design processes
- Facilitates continuous process improvement through knowledge capture and reuse
- Practicing structured design for manufacturing improves organizational learning and enables faster and smarter innovation
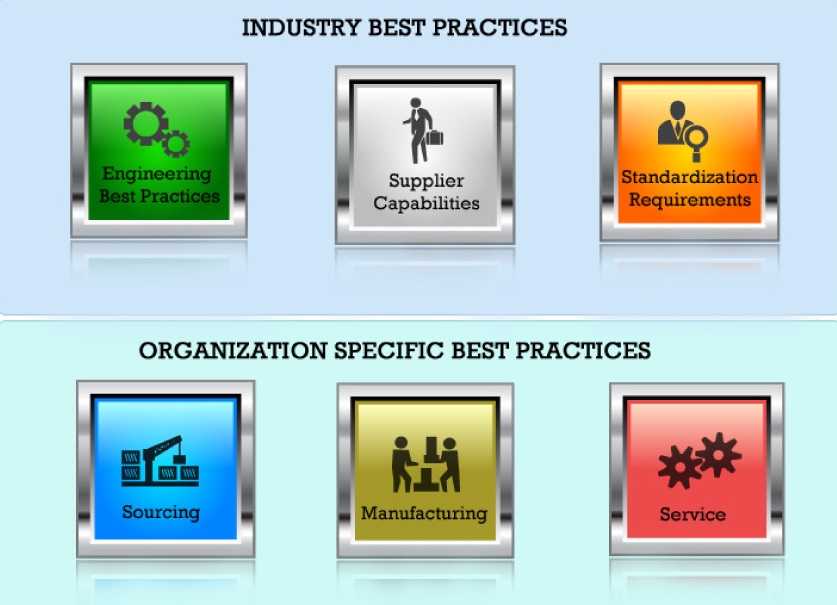
Quick Turnaround Time, Avoid Multiple Prototypes
In this pandemic, we have seen many reports of Additive Manufacturing (3-D printing) coming to the rescue with quick-turnaround times for parts like ventilator valves, personal protection equipment, and the like. As DIYers strived to react quickly to the need, it has taken many tries to perfect the part design to attain a manufacturable/printable component. The cost of redesign and iterations through redesign in these times is unaffordable.
- DFMPro integrated within popular CAD platforms, enables Design/Manufacturing Engineers to get the right designs confirming to the recommended guidelines for manufacturing processes like 3D Printing, Injection Molding, Assembly, Sheet Metal, Casting and many more.
- DFMPro helps to resolve manufacturability design problems thus minimizing prototyping time
- DFMPro works consistently every time using an industry standard set of rules and databases that capture and disseminate manufacturability knowledge
- Validate your 3D printing designs, minimize design iterations and introduce them as fit for manufacturing by saving time and cost
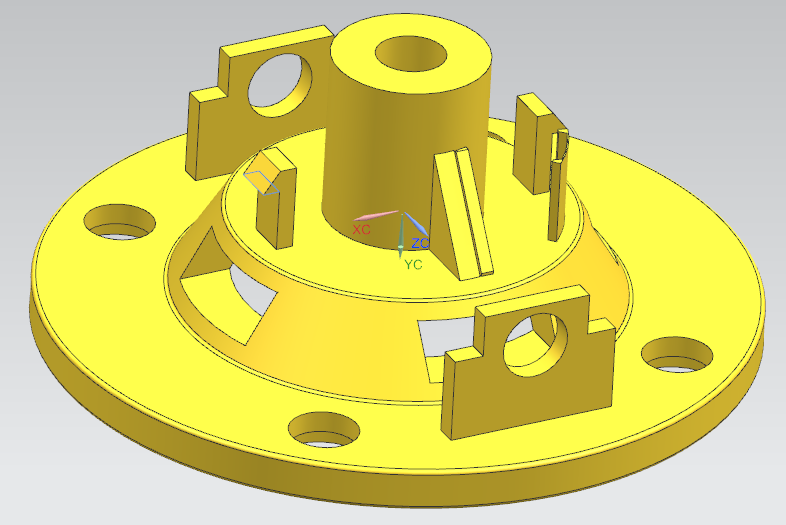
Get Early Visibility into Manufacturability and Product Cost
Today organizations spend millions of dollars over engineering change orders (ECO). A single ECO can cost up to $30,000.
DFMPro, an easy to use CAD integrated Design for Manufacturing (DFM) software, identifies & provides recommendations to resolve potential downstream manufacturing issues.
Helps reduce expensive and time-consuming design iterations resulting into faster development of high-quality products.
- Capture design issues early and reduce engineering rework
- Understand opportunities for cost reduction right at design stage and save cost
- Avoid late stage engineering changes and time-consuming rework
- Capture best practices and bring in standardization in design review process
Request a demo of DFMPro
DFMPro Delivers Results
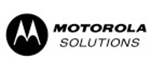
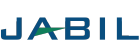
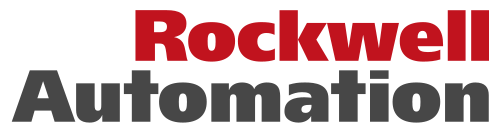