Automotive Manufacturing Industry Challenges
The global automotive market is undergoing its greatest transformation ever. As a result, automakers are exploring various approaches to autonomous driving and electric-powered vehicles, forcing them to alter their business models and product portfolios. However, heavy spending on new mobility and stagnation in key markets has pushed the automotive market into a profit desert. Some of the key automotive manufacturing industry challenges in the journey to profitability include:
Rising Product Complexity and Regulatory Requirements
- As the automotive manufacturing industry evolves, Mobility, Autonomous driving, Digitization, and Electrification will drive significant changes.
- Moreover, meeting regulatory requirements will increase engineering and R&D costs, requiring higher volumes to offset these expenses.
Declining Margins and Skill Shortage
- OEMs have kicked off additional cost reduction efforts, impacting supplier margins
- High investments required for trends like autonomous driving and electric mobility
- Required employee skill set is changing dramatically as the automotive manufacturing industry is moving towards digital transformation
Connected Supply Chain And Changing Role of Suppliers
- Digitizing the connected supply chain not only drives costs down but also engages consumers more effectively and enables better use of data to improve services
- To address these demands, suppliers must achieve the next wave of efficiency gains to overcome challenges and meet their goals.
DFMPro – a DFM for the Automotive Manufacturing Industry
By enabling engineering executives to make informed design decisions, DFMPro addresses downstream manufacturability, assembly, and quality challenges. Additionally, it captures and disseminates automotive manufacturing industry best practices, ensuring standardization across the organization.
Improve Time to Market and Cost by Reducing Engineering Change Orders (ECOs)
Reducing Engineering Changes (EC) is a Key Enabler for Improving Time to Market and Cost
- Studies conducted by SASIG shows that engineering change can cost anywhere from $5,000 to $7,500 per change
- DFMPro design for manufacturing solution enables EC reduction by addressing issues early during the design stage, thus reducing rework and improving Time-to-Market
Knowledge Capture and Reuse, Bring in Standardization
- DFMPro helps to capture and disseminate the automotive manufacturing industry best-practices and knowledge in form of DFx guidelines and brings in standardization across the organization
- Training new employees
Reduce Cost
- Identifying optimum design alternatives at early stage helps to reduce cost of the product
- Helps in removing inefficiencies and costs from all stages of the product lifecycle cycle to improve profitability and shrinking operating margins
Our Customers
Resources
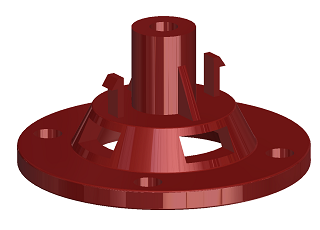
Automotive Plastics: Automate your way to efficient and high-quality Plastic part design with HCL’s powerful DFX solution
Learn how you can benefit from an automated DFX solution integrated into the CAD systems for best quality Injection Molded Plastic part design.
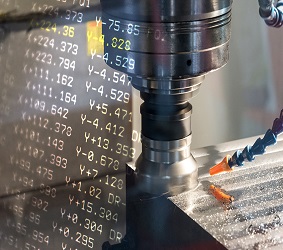
How HCL’s DFX Platform is Bringing in a Seismic Change to Efficient Design and Manufacturing
This webinar will help you deliver high-quality designs for manufacturing more quickly by using the new Design to Cost (DTC) module in DFMPro.
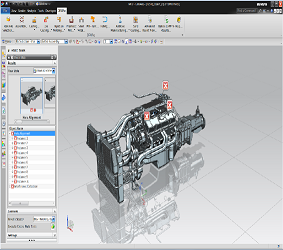
How design errors show up as tooling, processing, materials and abuse issues
For a plastic part or assembly to perform as expected, proper consideration must be given to material selection, part design, tooling, and processing using a holistic approach. In a lot of instances, desi-gn errors are mistaken as tooling, processing and material issues.
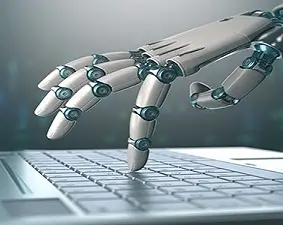
Why and How of DFM Review Automation
A DFM review automation tool helps in identifying areas in a design that are difficult, expensive or impossible to manufacture. It eases and reduces errors in the design validation process. Learn more in this whitepaper.