For a plastic part or assembly to perform as expected, proper consideration must be given to material selection, part design, tooling, and processing using a holistic approach. In a lot of instances, design errors are mistaken as tooling, processing and material issues. Design errors are even sometimes misclassified as customer abuse. The author conducted a Pareto analysis on the top 100 defects in molded parts that had the appearance of material, tooling, processing and customer issues and found that most of them could be traced back to fundamental issues in design. Some real examples will be shown to drive home the point. A possible solution to avoiding failures will be discussed. Key take ways from Webinar: - What is a Robust Design?
- Perform as Intended Over the Projected Life and Intended Environmental Conditions
- Meet the Appearance Requirements
- Be as Cost Effective as Possible
- A Holistic Approach to Robust Design
- Proper Consideration to Material, Design, Tooling and Processing
- Plastic Failure Factors
- Long Term Stress – a Common Thread
- A Pareto Analysis of Some of the Most Common Modes of Defects
- The Apparent and Real Causes for These Failures – Real Examples
- Poor Drying of Condensation Polymers – Solely a Processing Issue
- Introducing DFMPro
- How It Can Help Eliminate Most of the Failures Right at the Design Stage

| | Overview:Date: Jan 31, 2019 Time: 11:00 AM EST  Presenter: 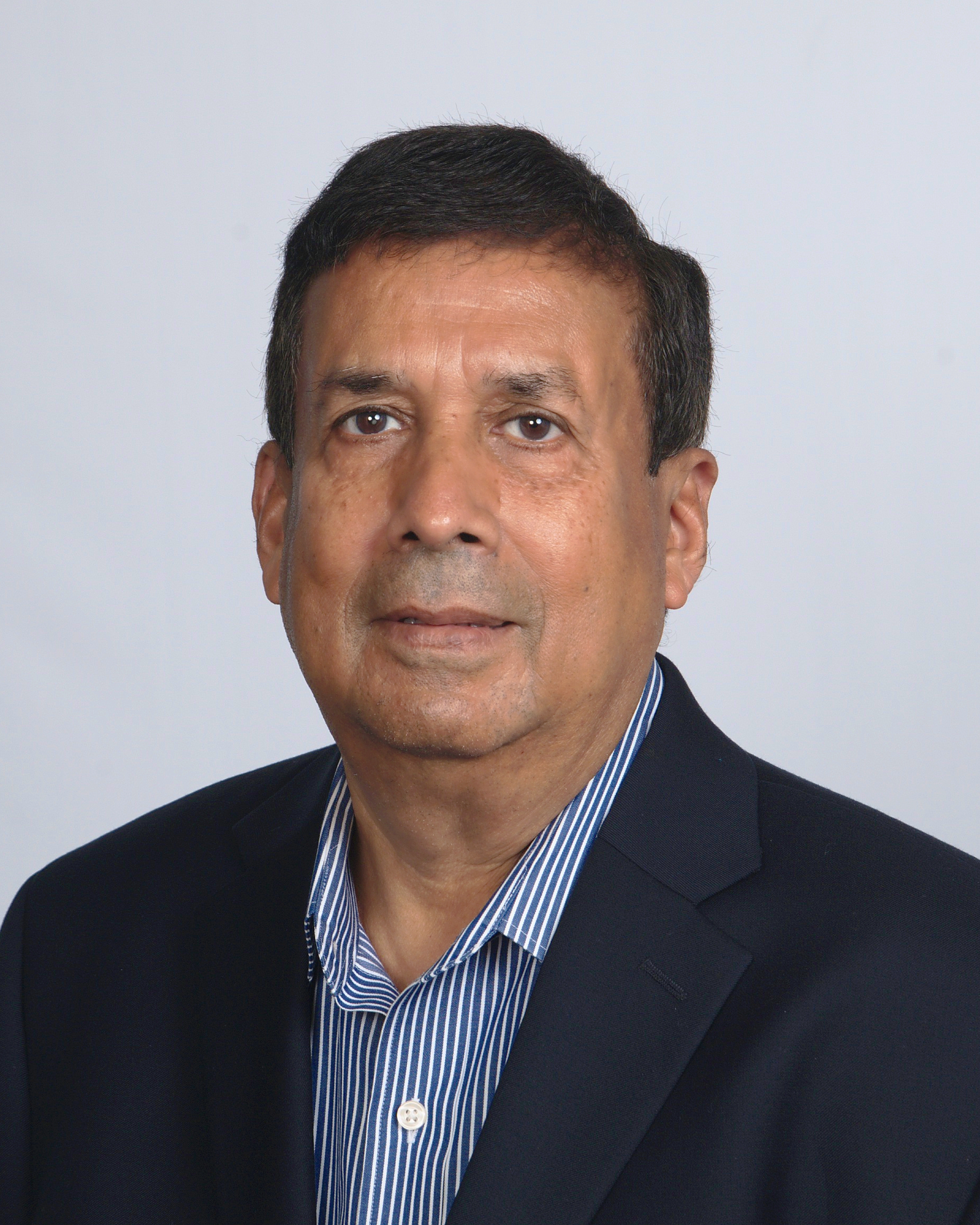 Vikram Bhargava Global Engineering Consultant, Author and trainer
Presenter: 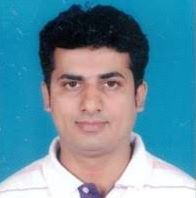
Yogiraj Dama Product Manager at HCL Technologies Ltd |