Participate in the survey to get a chance to win amazon gift card worth $100
No of Questions : 15 (Objective with easy to pick options)
Estimated Time: 4 mins
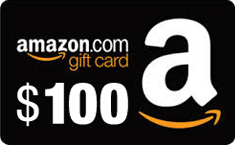
Background
From concept to manufacturing organizations make dozens of decisions that influence product outcome. Making better decisions sooner in the process typically drives better product and lower cost.
Design-for-manufacturing (DFM) or design-for-assembly (DFA) are not new concepts. What is new is a body of tools that bring awareness for things like manufacturing and assembly more directly into the original design environment.
Who Should Participate?
- VP/Director of Engineering
- Design managers
- Operation Managers
- Engineering Executives
- Operation Managers
- Engineering Managers
- Mechanical / Design Engineers
Why This Survey?
This survey will measure how organizations are moving towards DfX. Some organizations are already using one or more distinct DfX tools, some none. Some forward leaning teams are working on integrating various “X’s” into a common environment on their own or with software partners.
Based on various inputs like market survey, internal R&D, customer requests, an organization decides to bring a product to market. The first step of bringing a product to life is design. The design stage is probably the most important stage in the lifecycle of the product.
The design stage also involves the highest commitment to the final cost of the product. Many studies pointed out that while design stage takes a very short period in a product life cycle, it dictates around 70-80% of the product life cycle cost. Organizations have identified that if the product was designed such that it could be manufactured, assembled, serviced with ease, and quality was “built into the product”; then downstream and operational problems could be prevented. This has resulted in the design stage slowly gaining more importance in influencing downstream activities.
With this thought process, various concepts evolved which have guided organizations over time in designing products for ease of manufacturing, having better quality and costing less among others. “Design for manufacturing” (DfM) was one of the foremost among such concepts. Slowly, methods and techniques like Design for Assembly (DfA), Design for Quality (DfQ), Design for Six-Sigma (DfSS), Design for Serviceability, Design for Reuse, Design for Recycling, Design for Logistics (DfL), etc evolved. The recent focus is on Design for Environment or Design for Sustainability.
All these terms can be grouped under a generic name – Design for “X”, where X can be manufacturing, cost, reuse, sustainability, etc. On the other hand, X has also been used to represent excellence (Design for eXcellence). DfX provides means for collecting internal best practices, disseminating information and realizing the implementation of these practices. Design for eXcellence (DfX) is an organized way to systematically address the early involvement.
The objective of this survey is to seek individual feedback on the current DfX processes in organizations and establish a link with DfX process maturity. The questions do not focus on a specific area such as manufacturing or assembly but are generic covering process and framework maturity which may be applied to any and all DfX areas.