Holistic Design and How Focus on Cost During Design Will Help
Consideration of the following is required for a well-designed and cost-optimized plastic part or assembly:
- Material
- Design
- Tooling
- Processing, including Secondary Operations
This is analogous to the four wheels of a high-performance car.
In his book Failure of Plastics and Rubber [5], David Wright conducted an analysis on 5,000 failed parts and came up with the causes for the failures shown in the figure below.
Therefore, a designer may conclude that he or she is responsible for only twenty percent of the failures or cost overruns. What appears as materials, processing, tooling, or misuse issues may in a lot of cases can be traced back to fundamental design issues that may manifest themselves as the former
Let us look at a few examples:
Material
A plastic part cracks in use. We assume that it is the material weakness and change it to a different and possibly more expensive material. This not only makes the part more expensive, it also results in more engineering hours, more tooling, part qualification, inventory purge, etc.
In the example below, the reason for the crack was not the material (Polycarbonate). It was the sharp corner in the corresponding inside walls.
Design
Poor design, besides resulting in higher material, tooling and processing costs, will result in many avoidable costs and opportunity costs as described above.
Tooling
We often blame warpage, scuffing, poor filling, etc. on poor tooling. These may be the result of uneven walls, long thin walls, flow from thin to thick sections, inadequate draft angles, etc. In the picture below, the burn mark is supposedly due to poor venting. The fact is that the long thin rib allows the toolmaker no place to vent – clearly a design issue.
Processing
Thick sections because of poor design (rib thickness at the bottom, for example) lead to higher cooling time (proportionate to the square of the thickness). In smaller parts, this may add significantly to the overall costs.
Poor yields, not meeting the dimensions, warpage, flow marks, sink marks, etc. are often blamed on poor processing. The truth is that many of the issues are caused by design errors.
The flow marks and lack of filling in the example below (left) are caused by a thin area of plastic surrounded by thick area (hesitation effect). The ugly lines on the right are caused by thick ribs on the other side of the wall. No amount of adjustments can totally get rid of these issues. The result will be a substantially reduced yield resulting in higher costs.
DFMPro – A Design Assistant Solution
Organizations need to have a good sense of the cost early in the design stage and cannot wait until a supplier has been selected. DFMPro provides the tools to estimate and optimize the costs right from the early stages.
Two Sides of the Same Coin!
There are two aspects of design that impact costs, direct and indirect. The former consists of the material and direct manufacturing costs. Indirect costs are often hidden. These consist of costs such as ease of manufacturing, assembly, safety issues, etc. DFMPro provides a rule-based approach to provided information on both aspects.
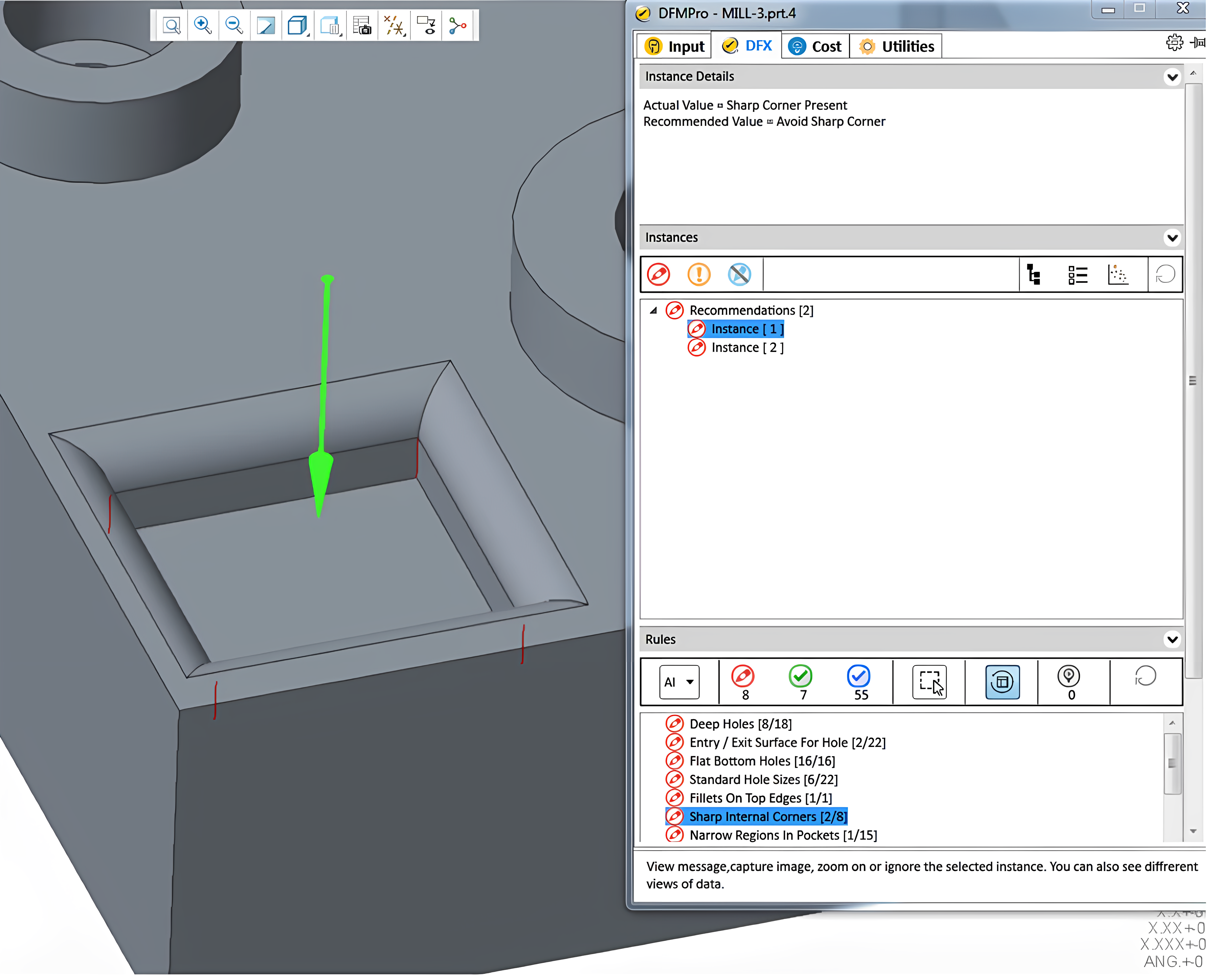
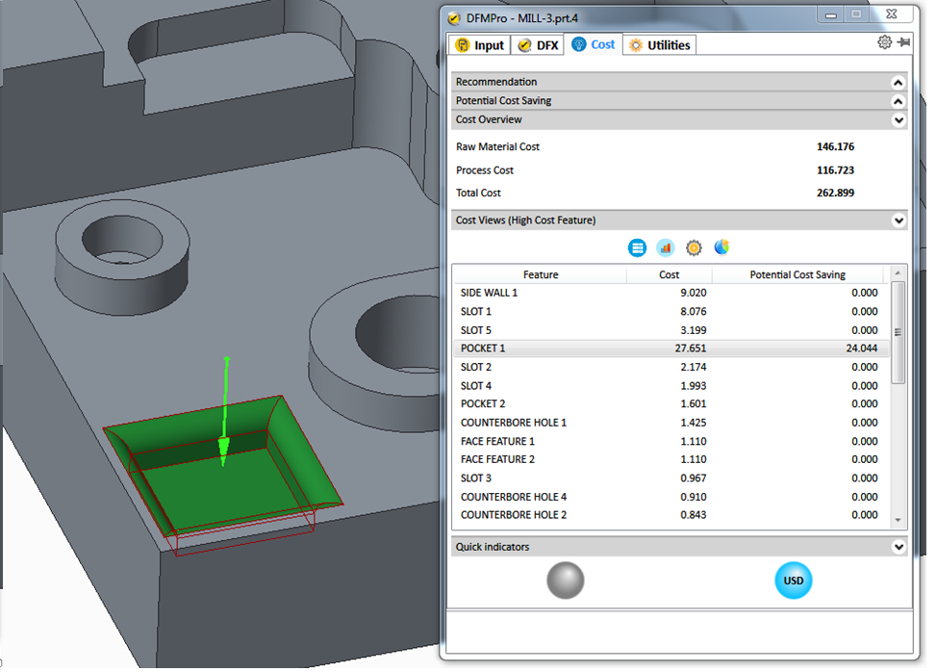