DFX and Cost Views
DFX View: DFX provides rule-based feedback. Organizational best practices that impact quality are configured in terms of smart checks, which, at the click of a button, provide quick feedback on areas of design that violate the best practices. It not only identifies problems but also suggests solutions to resolve the issues that will impact overall product costs. These impacts are primarily indirect through adverse impacts on quality or the addition of unnecessary complexity in manufacturing.
Examples
Case 1 : below depicts a thin steel condition. The combination of thin steel and sharp corners will result in a very weak condition requiring workarounds and/or frequent repair. This not only impacts the overall investment in tooling but also adds unnecessary downtime to the production process, resulting in additional costs.
Case 2 : below shows wall thickness as the parameter. The wall thickness here directly impacts the cooling time for each part. As stated before, the thickness increases the cooling time proportionately to the square of the thickness. Thus, if the cooling portion of the cycle time is 4 seconds for a 2 mm thick area, it will be 16 seconds for a 4 mm thickness in the same part!
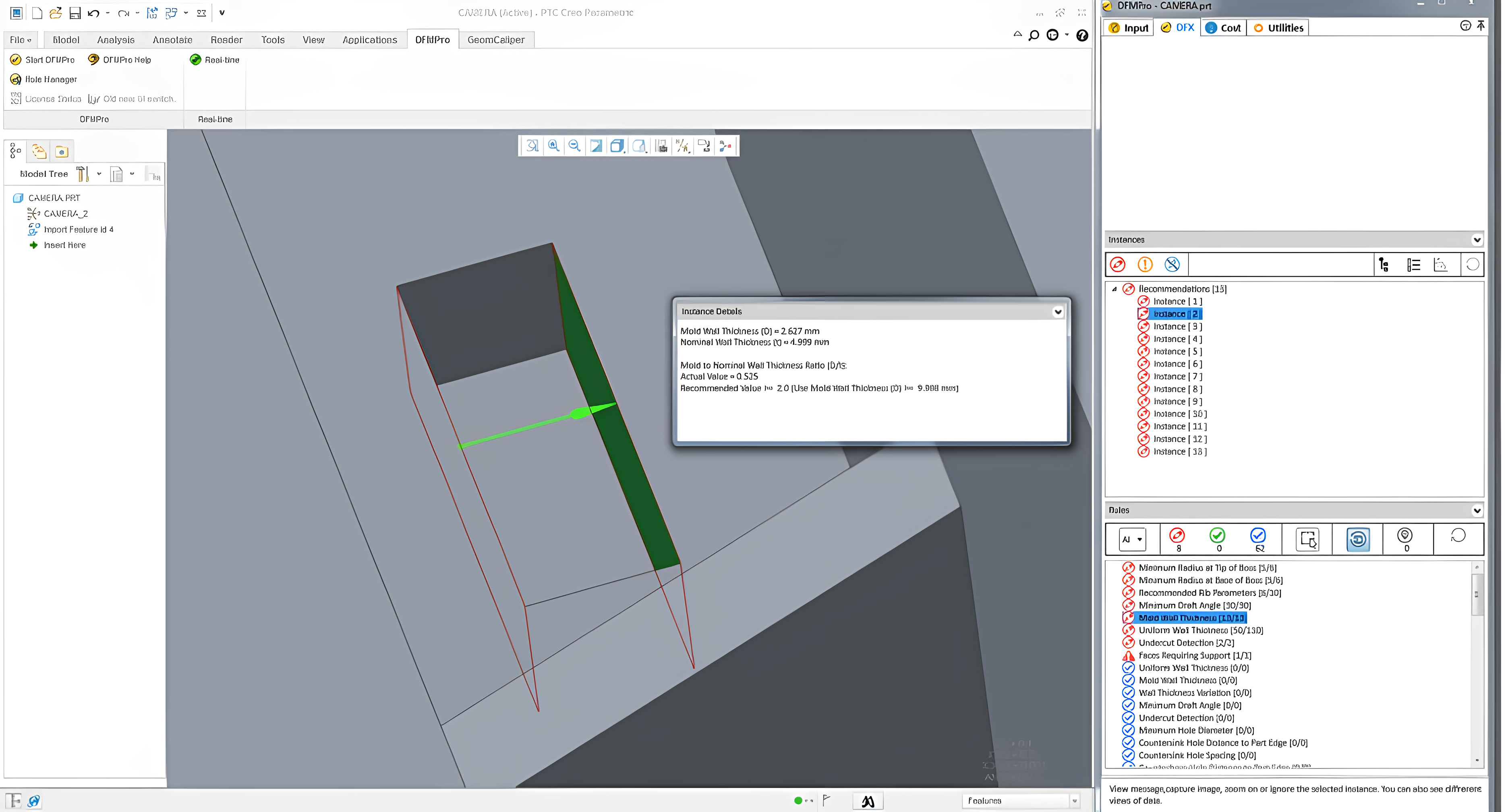
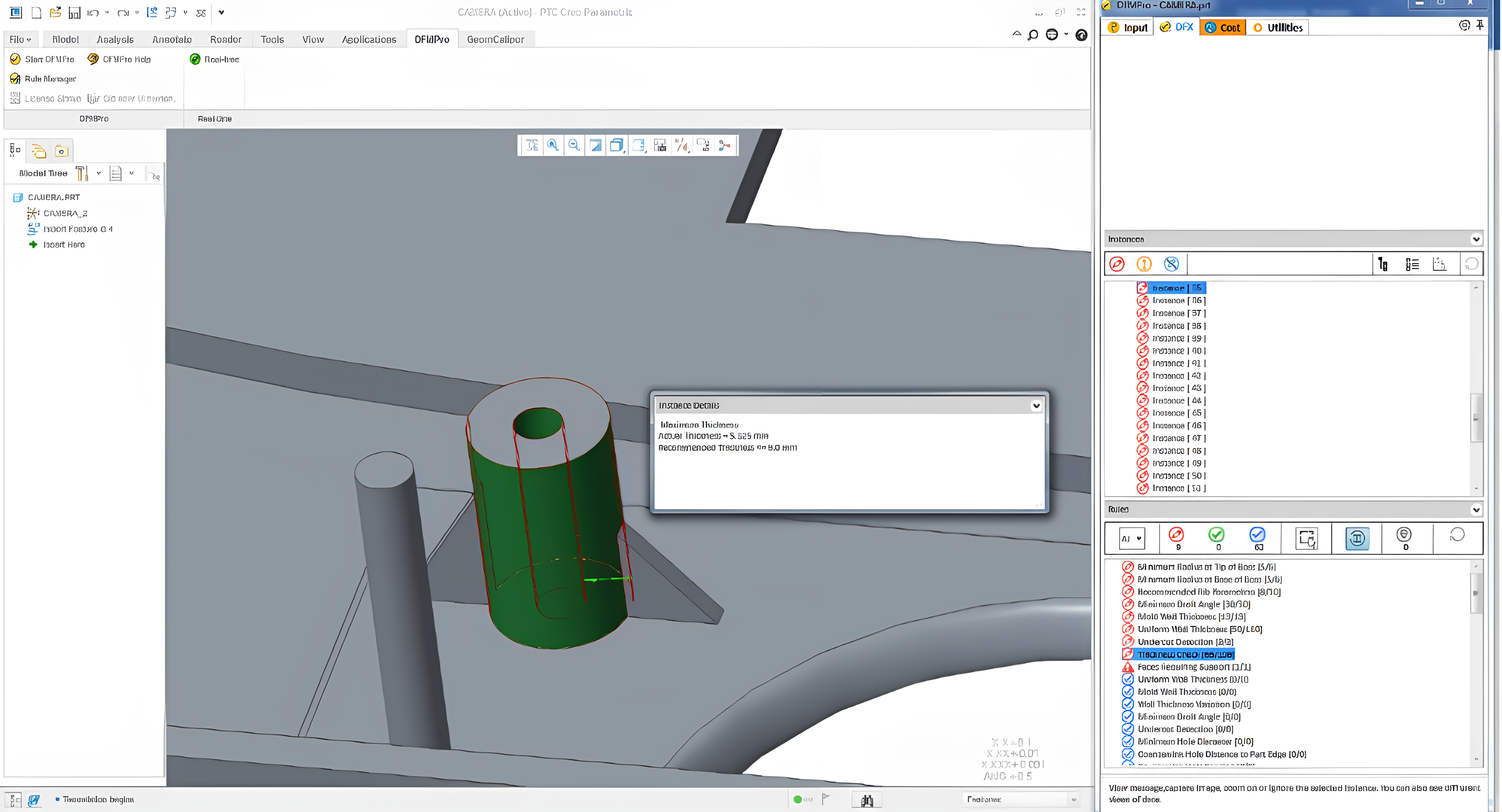
Hence, the first step for the design engineer, before looking at the cost determination, is to look at the DFM parameters of the design as they may impact the cost, which would be difficult to correct later.
Cost is the outcome of what gets decided at the design stage. The design engineer must make early decisions to keep the cost below target and optimize the design to balance the functional requirements and the product cost. This results in value being delivered to the customer. While functional requirements are a ‘must’ in design, it is also imperative to fully evaluate the various alternatives to achieve them.
Cost Breakdown
The cost of any manufactured product is divided into two broad areas: material and processing costs. Tool costs may also be amortized into the piece price.
Let us take the example of a Zinc (Zamak 3) motor bracket diecasting weighing about 25 gm being molded in a four-cavity tool. The tool’s total life is 1,000,000 shots. It is built out of H13 steel at a cost of $50,000.
The share of each part for this tool is 50,000/1,000,000/4 = 1.25 cents. Hence unless volume is very low, the tooling cost is not considered as part of total cost.
DFMPro cost addon shows this typical breakup of material and process cost to ensure that the design engineer is aware of adding every feature and how cost moves.
The following example depicts a typical chart in DFMPro for such cost breakdowns for the machined components.
Trade-offs:
inputs required to make these decisions may not be available initially. However, based on some initial assumptions, the Cost Add-on module can facilitate a quick evaluation of the options and help select the most suitable one for analysis. In addition to these options, even the design features impact cost. As a result, as features are updated, their respective impacts on cost are immediately shown. Tradeoffs may be required to maintain the price as the design progresses from initial to detailed design. With the built-in cost indicator, upward or downward cost trends can be automatically monitored.
Some of the options design engineers can use for trade-off purposes are:
- Material type and grade
- Manufacturing process chosen
- Manufacturing region (US, China, Europe, etc.)
- Special features
Apart from the above, there are process-specific options—for example, the type of runners (hot or cold) for injection molding or sheet metal cutting processes such as stamping dies, waterjets, plasmas, or lasers.
There are many variables in the design that impact manufacturing costs for features created on parts such as holes, slots, bends, sharp corners, fillets, etc. The impact of these is almost impossible to review manually during the design stages. This is where DFMPro shines by automatically sorting the costs allowing the designers to focus on the most robust design at the minimum cost.
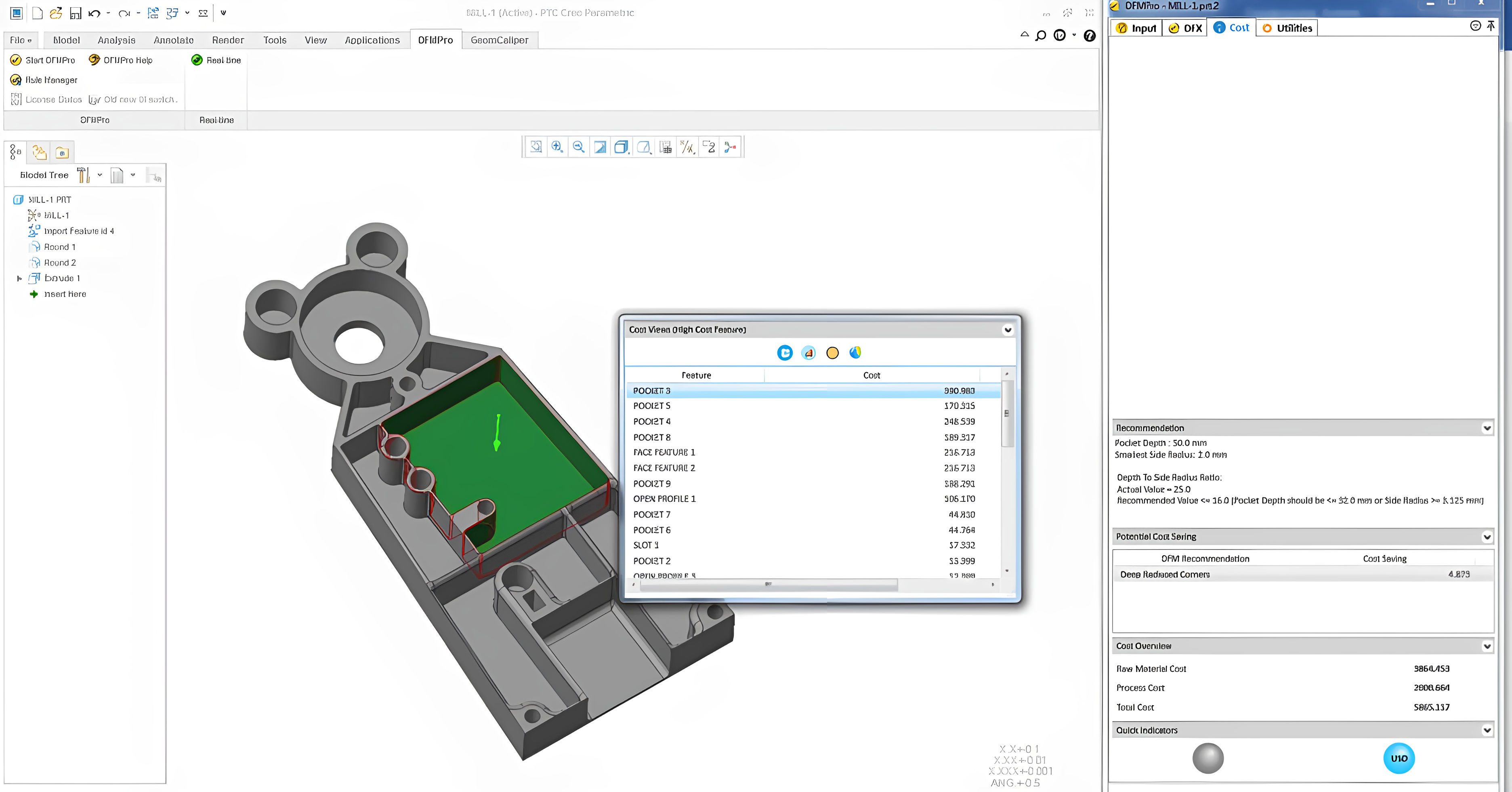
DFMPro is meant for design engineers to quickly evaluate design from the quality and cost point of view. The initial cost estimated at the time of design serves as a directional guide, and there are no surprises after the design is released for manufacturing. While not necessarily meant for negotiation purposes, its objective is to optimize the design along with the cost. It also reduces the time to design by providing an understanding of what parameters drive the cost and quality.
In a nutshell, DFMPro helps reduce rework, provides great visibility and control over costs, and ensures organizations meet their timelines for delivering great products.